New superfinishing milling cutter
for surfaces requiring grinding quality
Introducing the latest development from Mikron Tool, CrazyMill Cool SF, a high-performance endmill for superfinishing operations, which once again sets a benchmark in terms of surface quality: it finishes surfaces to grinding quality and enables the removal of subsequent grinding operations!
This is made possible by the perfect coordination of a state of the art milling concept which includes a tailored carbide substrate based on ultra-fine grain size, a highly efficient integrated cooling concept, and a cutting edge preparation which was specifically developed for superfinishing. In addition, there is a new cutting geometry that incorporates a variable helix angle and unequal angular teeth division.
As an example, in 316L stainless steel, CrazyMill Cool SF maintains a consistent surface quality below Ra 0.3 µm for more than seven (!) hours of machining time!
Available are two versions of endmills with five flutes (up to Ø 2.5 mm) and six flutes (from Ø 3 mm) in the diameter range from 1.0 – 8.0 mm (.039“ – .315“, fractional inches available). Type M for milling depths up to 3 x d and type N for 4 x d.
CrazyMill Cool SF - It's time to superfinish!
The challenge: Avoid and/or reduce subsequent polishing operations
Most machined components, need a post surface treatment like grinding, polishing, or tumbling. Those manufacturing steps can be very costly and very time consuming. Improving the surface quality through the superfinishing milling process makes it possible avoid or reduce subsequent finishing operations.
The solution: Mill surfaces below Ra 0.3 µm
The new CrazyMill Cool SF milling cutter is characterized by extremely smooth and sharply ground cutting edges, variable helix angle, variable pitch, and a high number of teeth. These features enable low radial cutting pressure and extremely smooth cutting, resulting in milled surfaces of grinding quality. After machining, the surfaces have an astonishing roughness value of Ra 0.3 µm or better in milling direction (Ra parallel,) and endmill axis direction (Ra 90°).
This shortens the manufacturing process, by avoiding or reducing significantly the post-surface treatment.
Real case: Watch Industry Ti Gr5 (3.7165)
Real case: Hemostatic clamp 17-4 PH

Real case: Radius compression plate Ti Gr.2 (3.7035)
Tool miniaturization
The challenge: Tool miniaturization
The miniaturization of milling tools brings with it the challenge of realizing the highly complex cutting geometries of milling tools even with diameters of less than 3 mm. The greatest challenge is to grind these complex geometries on small milling cutter cross-sections with a high number of flutes and at the same time to meet the highest quality requirements for the milling cutters in series with process reliability.
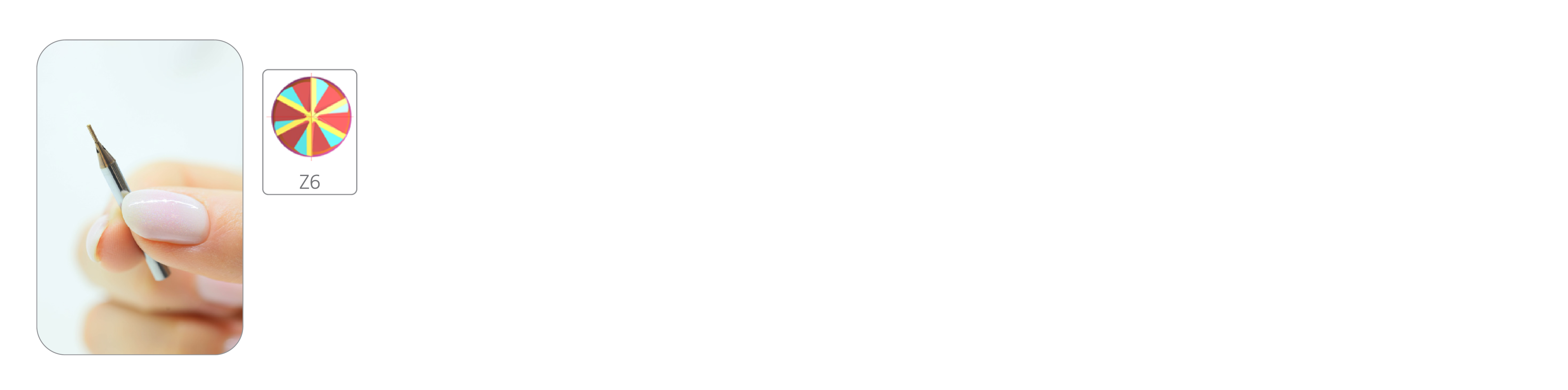
The solution: Highly skilled machine operators and suitable production equipment
State-of-the-art grinding machines with hydrostatic bearings and superior grinding wheel technologies, are crucial to produce the latest micro-tools. High-precision digital measuring devices which can detect deviations of up to one micrometer are also a necessity. The production team at Mikron Tool has mastered these processes and is exceptionally trained in applying these superior skills to the micro range. The quality standard of the high-performance milling cutters is correspondingly elevated, producing the exacting quality guaranteed by and expected from Mikron Tool.
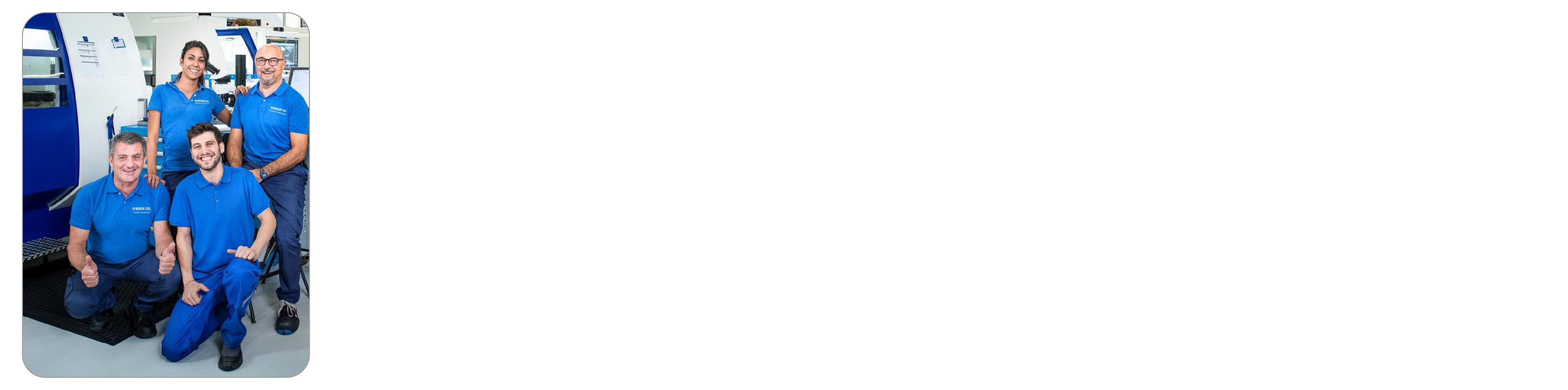
Avoid chattering when milling
The challenge: Avoid chattering when milling
Milling is a cutting process with a continuous interrupted cut. Each cutting edge applies a certain amount of pressure to the material. When the cutting edge exits the material,
the pressure is released again.
This happens with all the cutting edges of symmetrically designed endmills at a predetermined frequency depending on the “number of cutting edges” x “speed”.
If the frequency is kept uniform (see diagram) (TZ1 = TZ2 = TZ3 = TZ4), it can lead to an increase in the maximum deflection in the resonance frequency, resulting in vibrations and consequently
chatter marks on the workpiece.
Dynamic regular
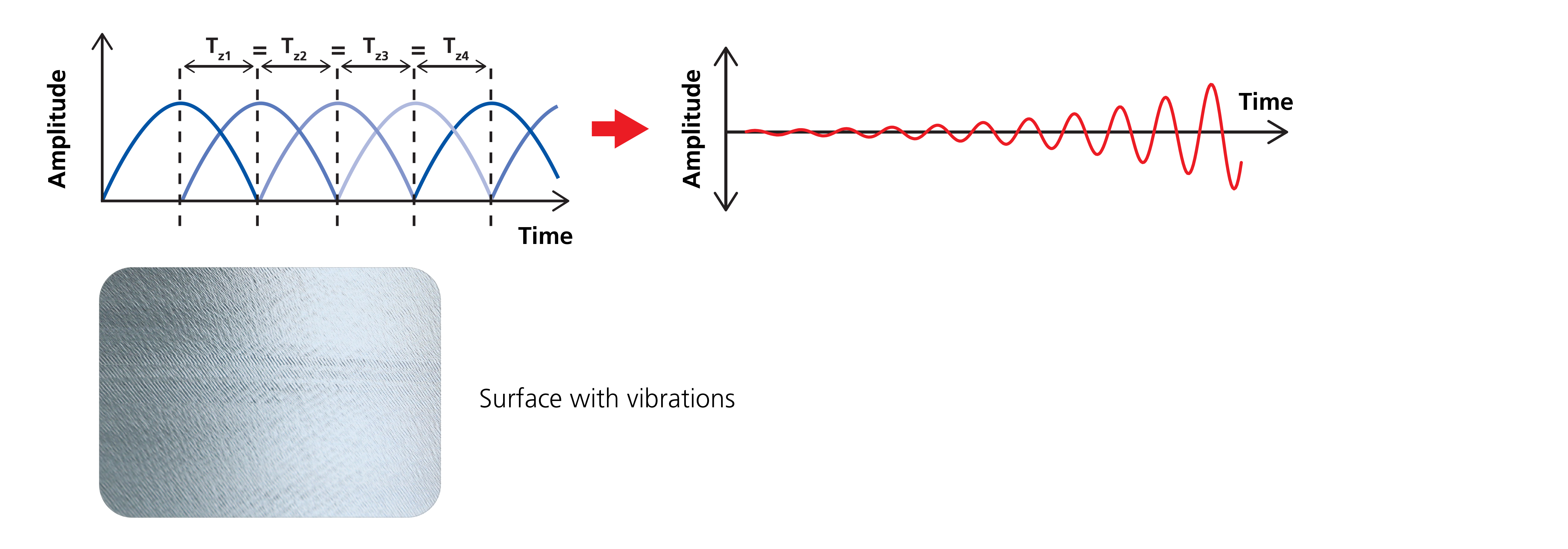
The solution: Avoidance of resonance frequencies
The new CrazyMill Cool SF has specific macro and micro geometries that suppress resonance frequencies. Two key elements are decisive here: firstly, an unequal angular teeth division and secondly, a variable helix angle per cutting edge (each cutting edge has a different helix angle).
As a result, none of the cutting edges generate the same frequency (TZ1 ≠ TZ2 ≠ TZ3 ≠ TZ4).
As shown in the diagram, these measures prevent the formation of resonance frequencies and thus enable chatter-free surfaces over the entire engagement length of the milling cutter.
Dynamic irregular
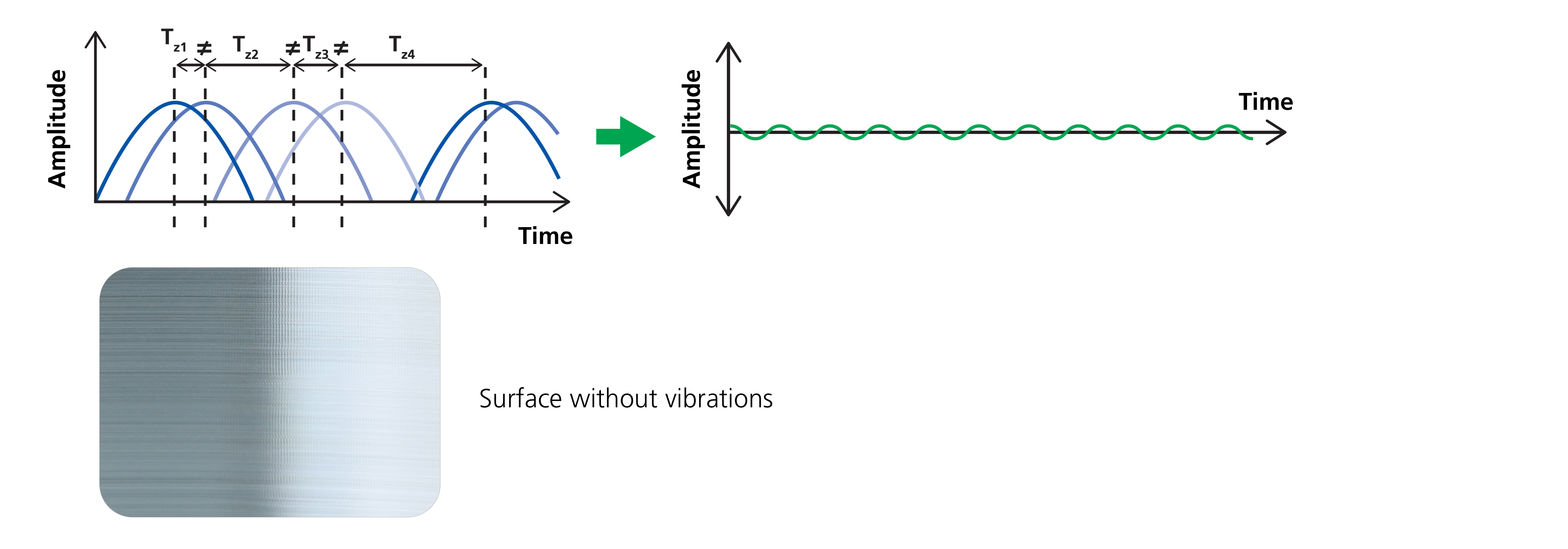
An all-round high-performance endmill for all materials
The challenge: An all-round high-performance endmill for all materials
Materials present a vast variety of mechanical characteristics. Different levels of toughness, hardness, and grain structure can drastically affect the material’s machinability. The best result can be achieved with a macro and micro cutting-edge geometry that is specifically tailored to the respective material. It is a great challenge to develop a cutting-edge geometry that is suitable for the most commonly used materials in the advanced machining sector, while at the same time achieving an outstanding surface quality comparable to grinding.
The solution: Mikron Tool’s last innovative product
Our “crazy” R&D department developed the new endmill CrazyMill Cool SF for super finishing with one unique cutting geometry. Thanks to this "crazy" development, the CrazyMill Cool SF achieves a surface roughness of less than Ra 0.3 µm and delivers outstanding shape accuracy on the workpiece. In addition, the CrazyMill Cool SF guarantees a remarkable tool life and extremely fast machining in all the materials shown below.
High temperature & chips in the cutting zone
The challenge: High temperature & chips in the cutting zone
The machining of metals requires a high energy input into the cutting zones. A large proportion of this is converted directly into thermal energy. The higher the heat generated in the cutting zone, the shorter the tool life. It is therefore essential to keep the temperature in the cutting zone as low as possible. A high machining temperature also leads to poorer chip formation, poor chip flow and poor chip evacuation due to the higher plasticity of the chip, which can result in chip jam. These phenomena are exacerbated in materials that are difficult to machine, such as titanium, stainless steel and heat-resistant alloys.
The solution: Integrated cooling in the shank
The patented cooling channels of the Mikron Tool milling cutters, which run through the shank, ensure constant and massive cooling of the cutting edges. The excellent cooling performance directly in the cutting area enables a much higher cutting speed and also reduces wear enormously. The massive coolant jet (from just 15 bar) also guarantees a chip-free machining zone and prevents the chips double cut. Higher cutting speeds, in combination with an HDM strategy, lead to a reliable milling process with a high removal rate while maintaining excellent surface quality.
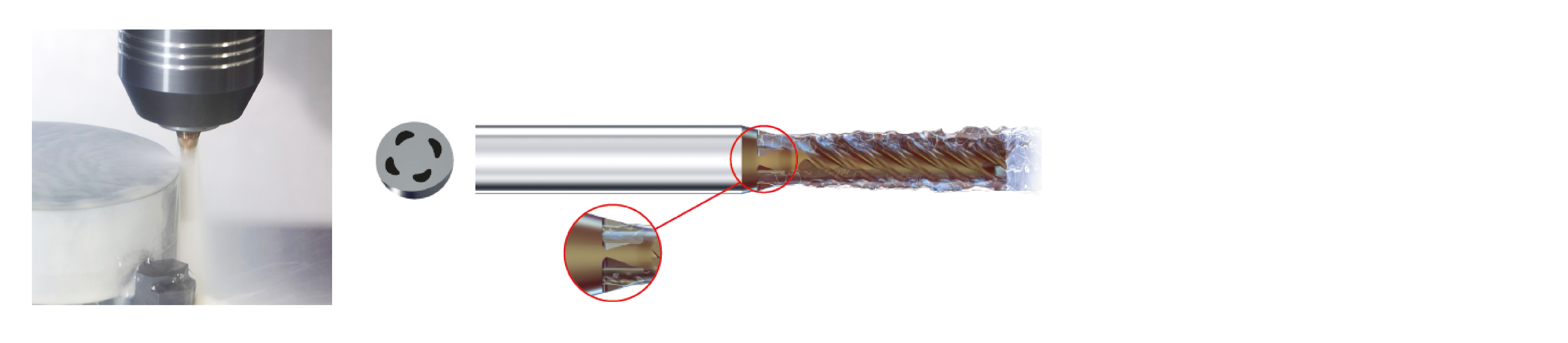
ONE Superfinishing milling cutter for all materials
The challenge: ONE superfinishing milling cutter for all materials?
The main challenge is to consistently preform high-quality and high-precision workpieces, with the highest demands on surface quality with a Ra (both directions) of less than 0.3µm, in a variety of material. To add to the challenge, it was a requirement to provide an endmill which offered high feed rates and excellent tool life.
The solution: CrazyMill Cool SF
The development goal for the CrazyMill Cool SF superfinishing milling cutter was the solution to an universal tool that achieves surface finishes in grinding quality below Ra 0.3µm in a wide range of materials. Thanks to the technical features of the milling cutter, the result is simply outstanding. See also the overview!
The CrazyMill Cool SF superfinishing milling cutter is the new benchmark in superfinishing precision micro milling. CrazyMill Cool SF: Developed and produced by the “crazy” people from Agno.
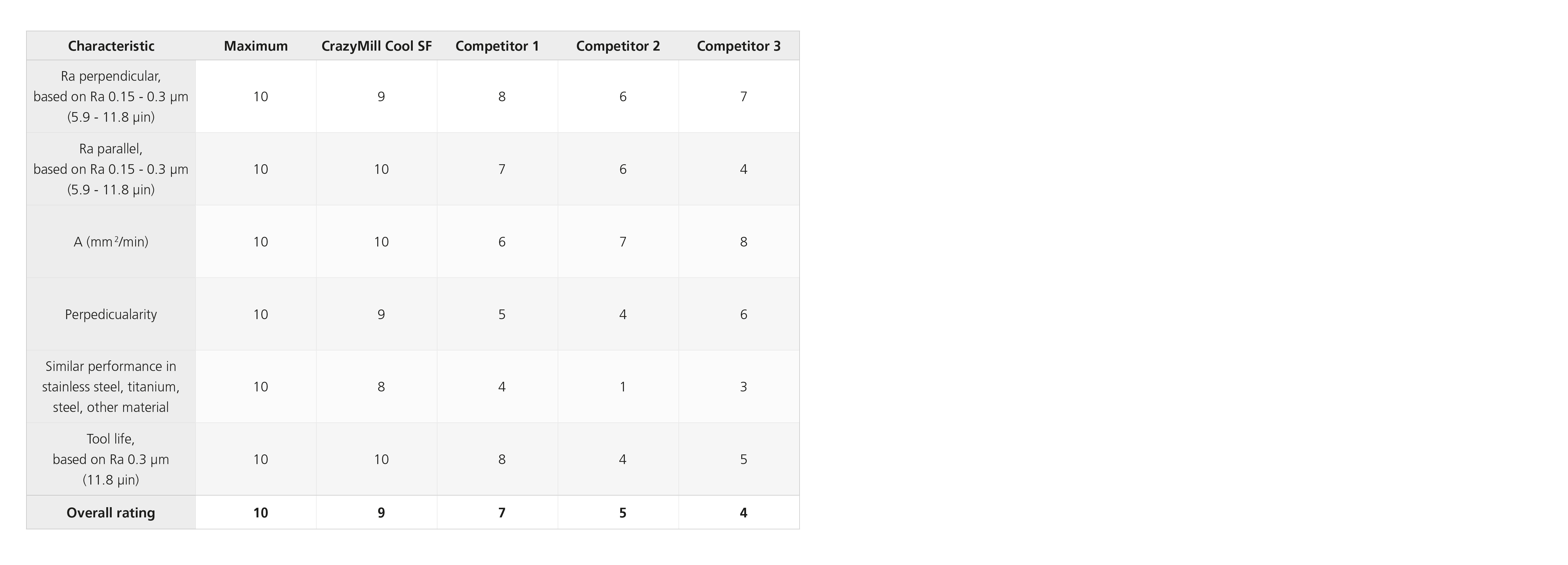
Your personal CrazyMill Cool SF
Mikron Tool also offers CrazyMill Cool SF in customer-specific executions:
- Milling cutters with varying diameters, lengths and teeth to the standard milling program / sizes
Do you need more information about our possibilities? Contact us here.
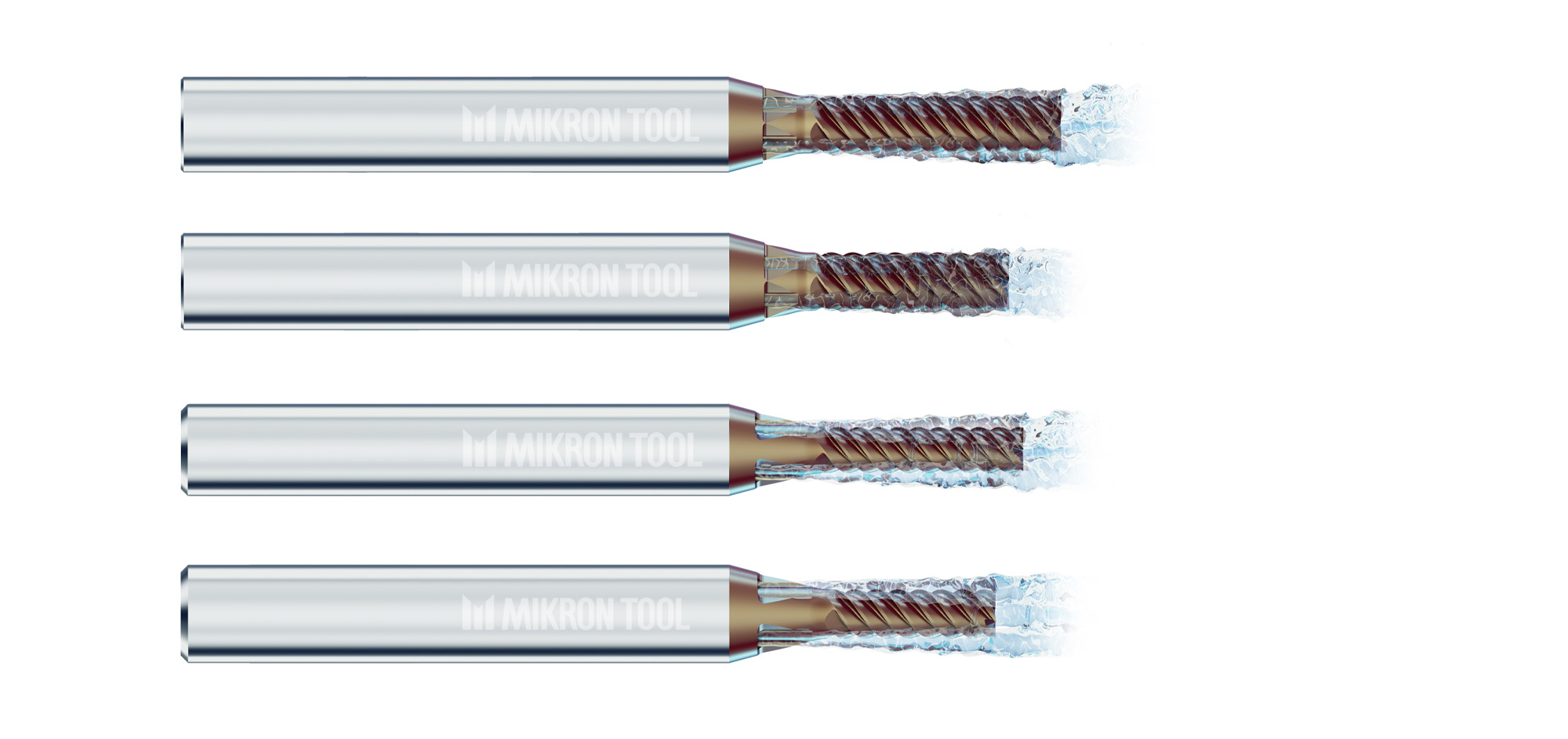