High-performance milling
with excellent surface quality
CrazyMill Cool CF, the latest generation of milling cutters from Mikron Tool, works with minimal side milling cutting pressure resulting in completely chatter-free machining. The result is an excellent surface quality (Ra 0.5 µm or better).
This is made possible by an ingenious cutting-edge geometry which enables highly dynamic milling processes. The milling cutter really comes into its own with thin-walled, delicate workpieces that tend to vibrate or when unstable clamping situations prevail. Pockets and grooves can also be produced efficiently, accurately, and with high-quality surface finish. This applies to all materials, from carbon steel to difficult-to-machine materials as stainless steel, titanium, and superalloys; the CrazyMill Cool CF is the solution.
CrazyMill Cool CF, square and corner radius endmill, is available in two variants: Variant 1 has four flutes (up to Ø 2.5 mm) and Variant 2 has five flutes (from Ø 3 mm). The diameter range is 1.0 – 8.0 mm (.039” – .315”, with fractional sizes available) and there are two options for cutting lengths of 3 x d and 4 x d.
Avoid chattering when milling
The challenge: Avoid chattering when milling
Milling is a cutting process with a continuous interrupted cut. Each cutting edge applies a certain amount of pressure to the material. When the cutting edge exits the material,
the pressure is released again.
This happens with all the cutting edges of symmetrically designed endmills at a predetermined frequency depending on the “number of cutting edges” x “speed”.
If the frequency is kept uniform (see diagram) (TZ1 = TZ2 = TZ3 = TZ4), it can lead to an increase in the maximum deflection in the resonance frequency, resulting in vibrations and consequently
chatter marks on the workpiece.
Dynamic Regular
The solution: Avoidance of resonance frequencies
The new CrazyMill Cool CF has specific macro and micro geometries that suppress resonance frequencies. Two key elements are decisive here: firstly, an unequal angular teeth division and secondly, a variable helix angle per cutting edge (each cutting edge has a different helix angle). As a result, none of the cutting edges generate the same frequency (TZ1 ≠ TZ2 ≠ TZ3 ≠ TZ4).
As shown in the diagram, this strategy prevents the formation of resonance frequencies and thus enable chatter-free surfaces over the entire engagement length of the milling cutter.
Dynamic Irregular
High removal rate
The challenge: High removal rate for thin-walled and unstable workpieces
Thin-walled workpieces such as blades, medical bone plates, and others, are among the most difficult components to machine. The reason for this is that with “unstable workpieces”, the cutting forces exerted by an endmill during side milling lead to deformations and vibrations. The result are irregular profiles and chatter marks. To avoid such consequences, low axial and radial engagement are typically set and a low feed rate is also used. The disadvantage is a very low material removal rate (Q).
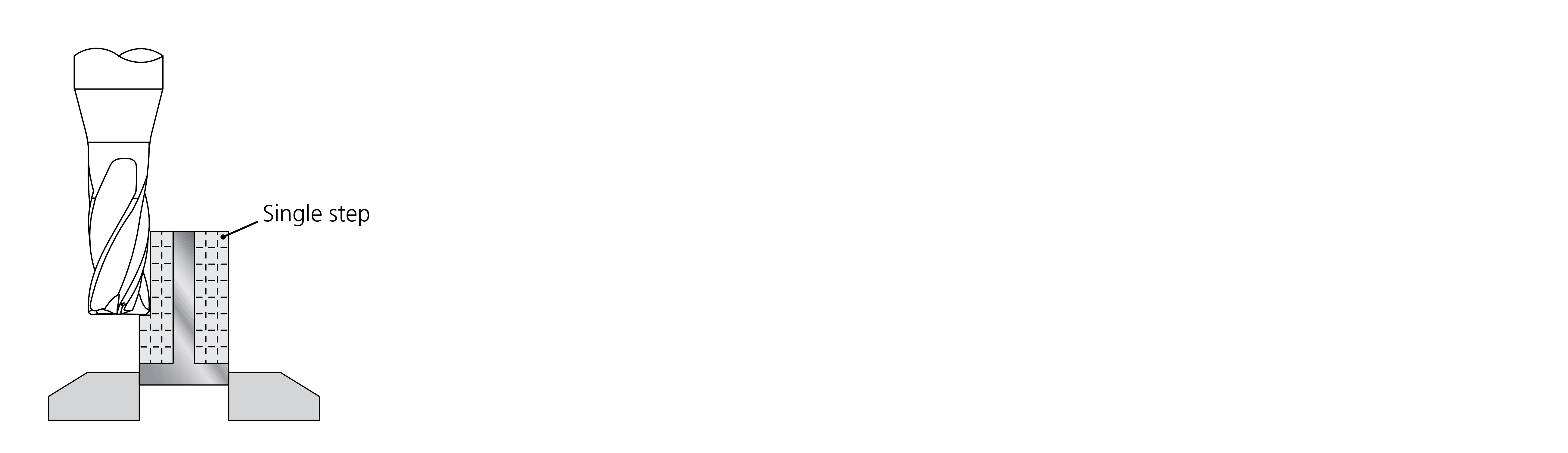
The solution: Low radial pressure
With the new endmill, particular attention has been placed to finding a perfect balance between cutting angle, a relief angle, and the conditioning of the cutting edge.
Elevated cutting capability ensures a very low lateral cutting pressure, so that the endmill can cut reliably even at its maximum axial engagement (4 x d). A large, or maximum, axial engagement, combined with a highly dynamic milling strategy (HDM), enables a very high material removal rate (Q).
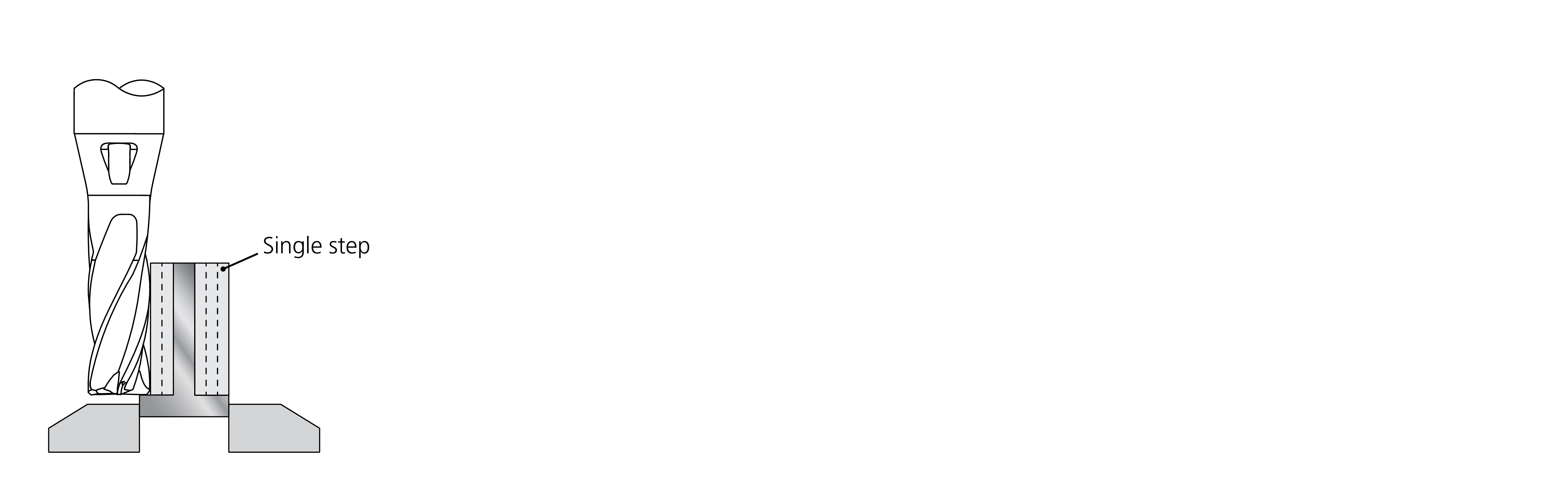
High shape tolerance
The challenge: High shape tolerance - perpendicularity
Profile milling with the side milling strategy over the maximum engagement length of the milling cutter (4 x d) must result in a perfectly perpendicular profile within the specified tolerance fields. This must also be achievable when using high-speed and highly dynamic milling strategies.

The solution: Low radial cutting forces
Thanks to its specifically designed micro and macro cutting geometries, CrazyMill Cool CF ensures a very low lateral cutting pressure, which is crucial for keeping the cutting forces perpendicular to the component low. This is a prerequisite for limiting the deflection of the milling cutter to a minimum and thus guaranteeing the shape tolerances and squareness in accordance with the required tolerance values, even at the maximum depth of engagement of the milling cutter.
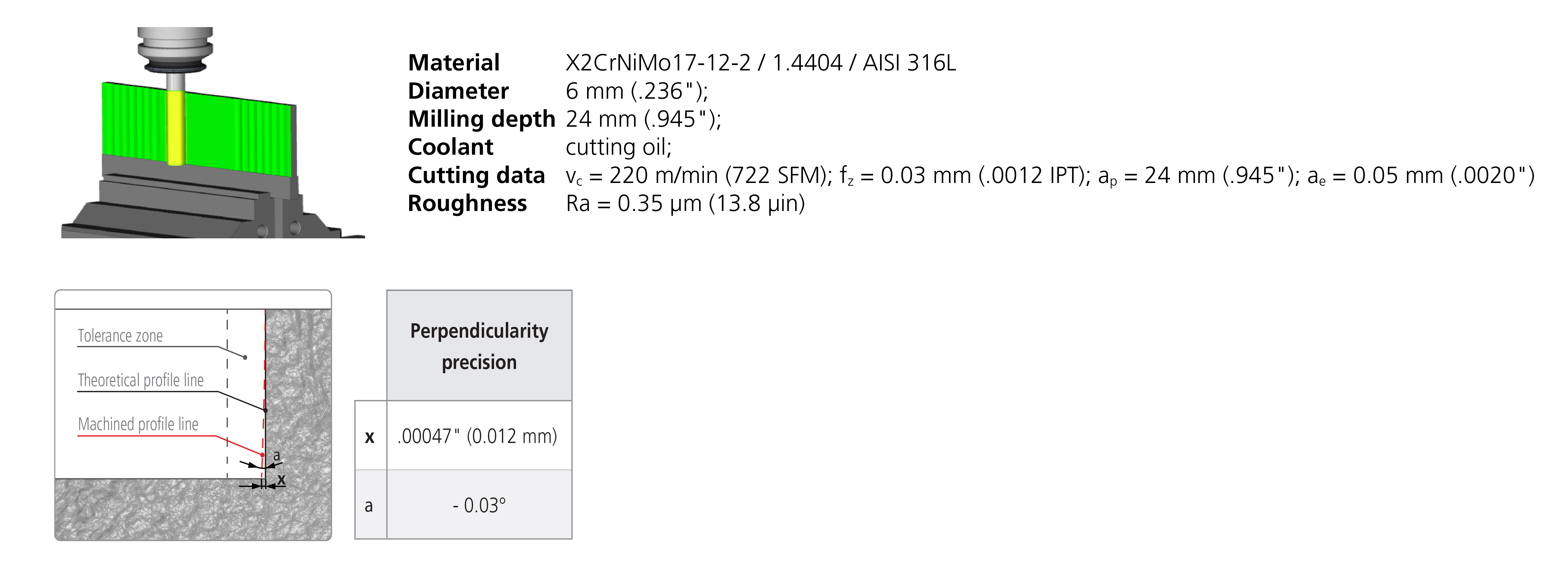
High surface quality
The challenge: High surface quality – process reliable chip management
For a reliable machining process, short chips are required. The more axial engagement of the endmill the longer become the chips. Long chips are very hard to manage and evacuate, generating a high risk of ”double-cutting”, leading to cutting edge chipping and/or to a low surface's quality.
The solution: Optimized chip-splitting for short chips and perfect surface quality
Chip-splitting design
The shape of the chip-splitting has been optimized to ensure short chips and optimum removal. The result is a perfect surface quality.
Surface quality
Thanks to the chip-splitting, no groove is visible, as would be the case when using a conventional milling cutter. The result is the best surface quality.
High temperature & chips in the cutting zone
The challenge: High temperature & chips in the cutting zone
The machining of metals requires a high energy input into the cutting zones. A large proportion of this is converted directly into thermal energy. The higher the heat generated in the cutting zone, the shorter the tool life. It is therefore essential to keep the temperature in the cutting zone as low as possible. A high machining temperature also leads to poorer chip formation, poor chip flow and poor chip evacuation due to the higher plasticity of the chip, which can result in chip jam. These phenomena are exacerbated in materials that are difficult to machine, such as titanium, stainless steel and heat-resistant alloys.
The solution: Integrated cooling in the shank
The patented cooling channels of the Mikron Tool milling cutters, which run through the shank, ensure constant and massive cooling of the cutting edges. The excellent cooling performance directly in the cutting area enables a much higher cutting speed and also reduces wear enormously. The massive coolant jet (from just 15 bar) also guarantees a chip-free machining zone and prevents the chips double cut. Higher cutting speeds, in combination with an HDM strategy, lead to a reliable milling process with a high removal rate while maintaining excellent surface quality.
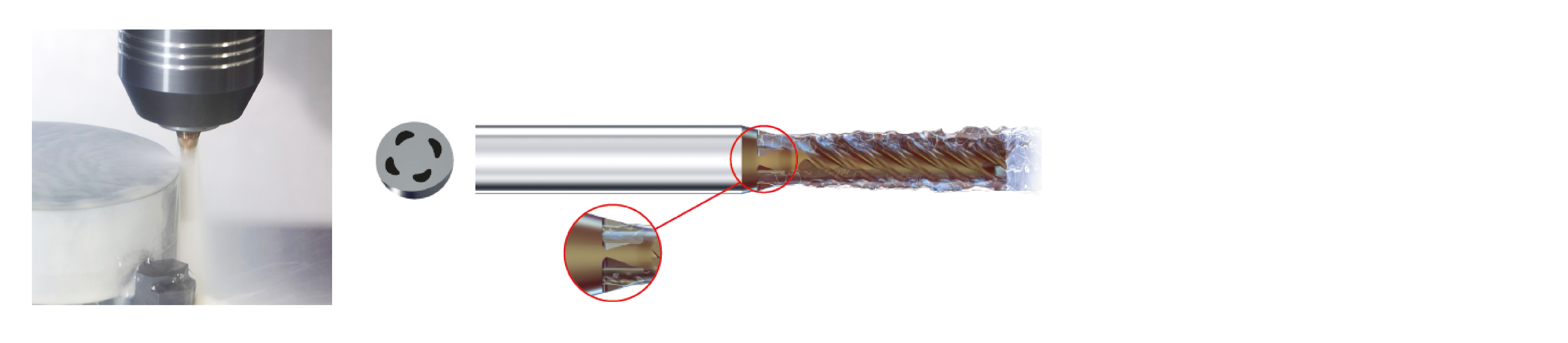
Your personal CrazyMill Cool CF
Mikron Tool also offers CrazyMill Cool CF in customer-specific executions:
- Milling cutters with varying diameters, lengths and teeth to the standard milling program / sizes
Do you need more information about our possibilities? Contact us here.
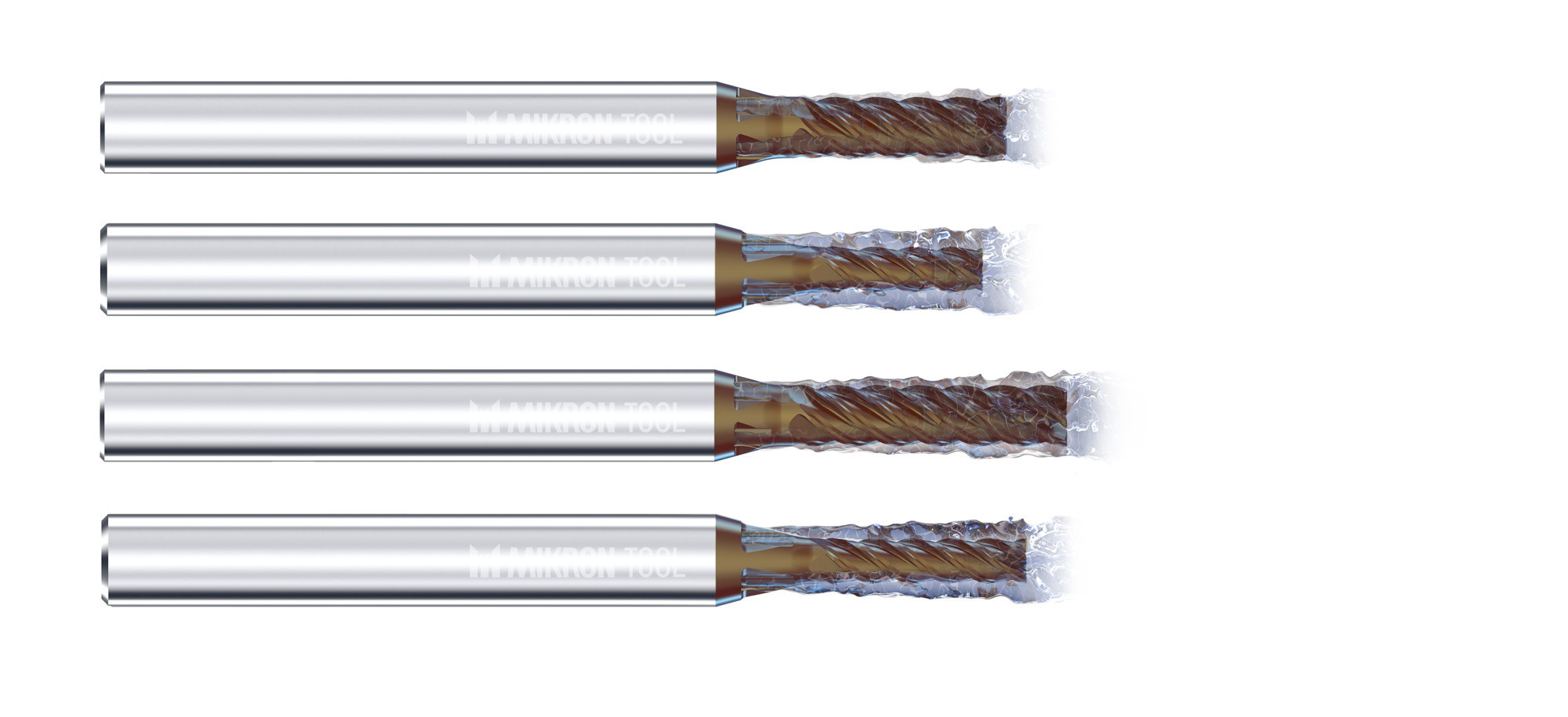