Hybrid manufacturing strategy for reverse shoulder prosthesis component
The development specialists at Mikron Tool in Agno, partnering with DMG MORI and supported by Motorex’s cooling lubricant experts, have developed a hybrid process to optimize the manufacture of a “glenoid base plate” (titanium component of a reverse, cementless shoulder prosthesis). This was completed in a three-step process: solid base machined on a millturn-machining center, implant post printed on 3D SLM machine, and final machining completed on a traditional vertical machining center.
The hybrid process has the potential to become well established in prosthesis production. Compared to traditional manufacturing processes, there are economic and qualitative advantages.
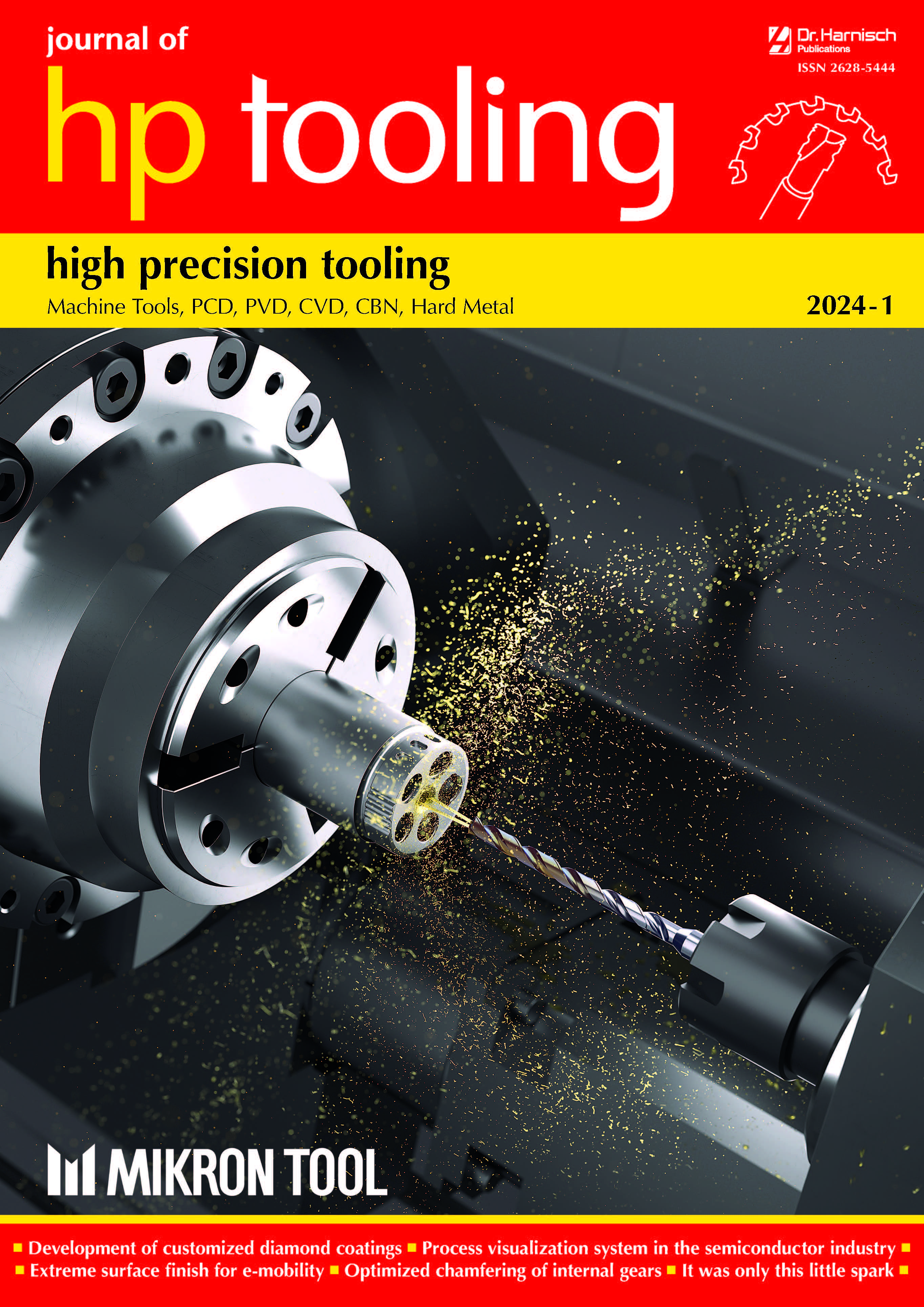
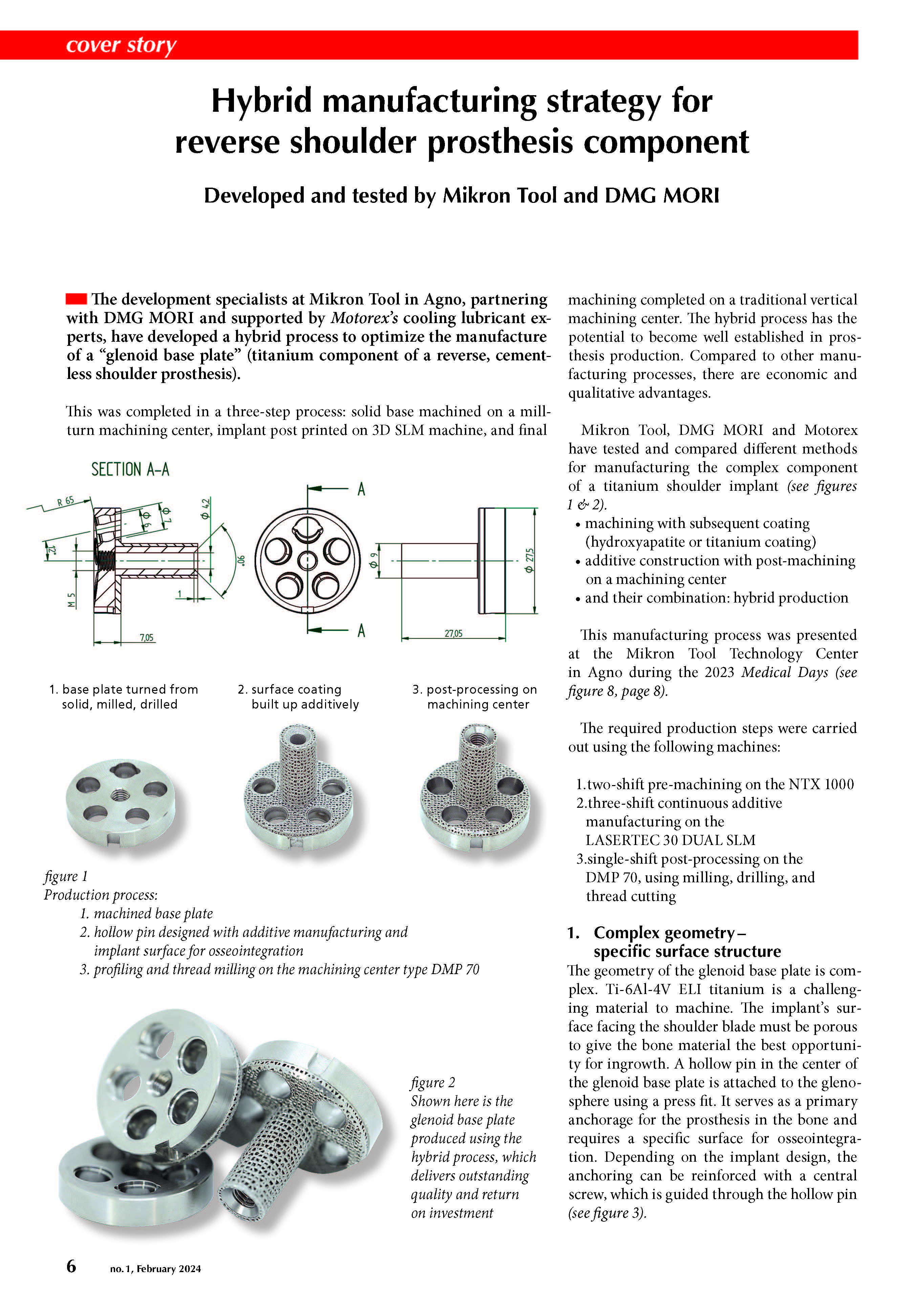
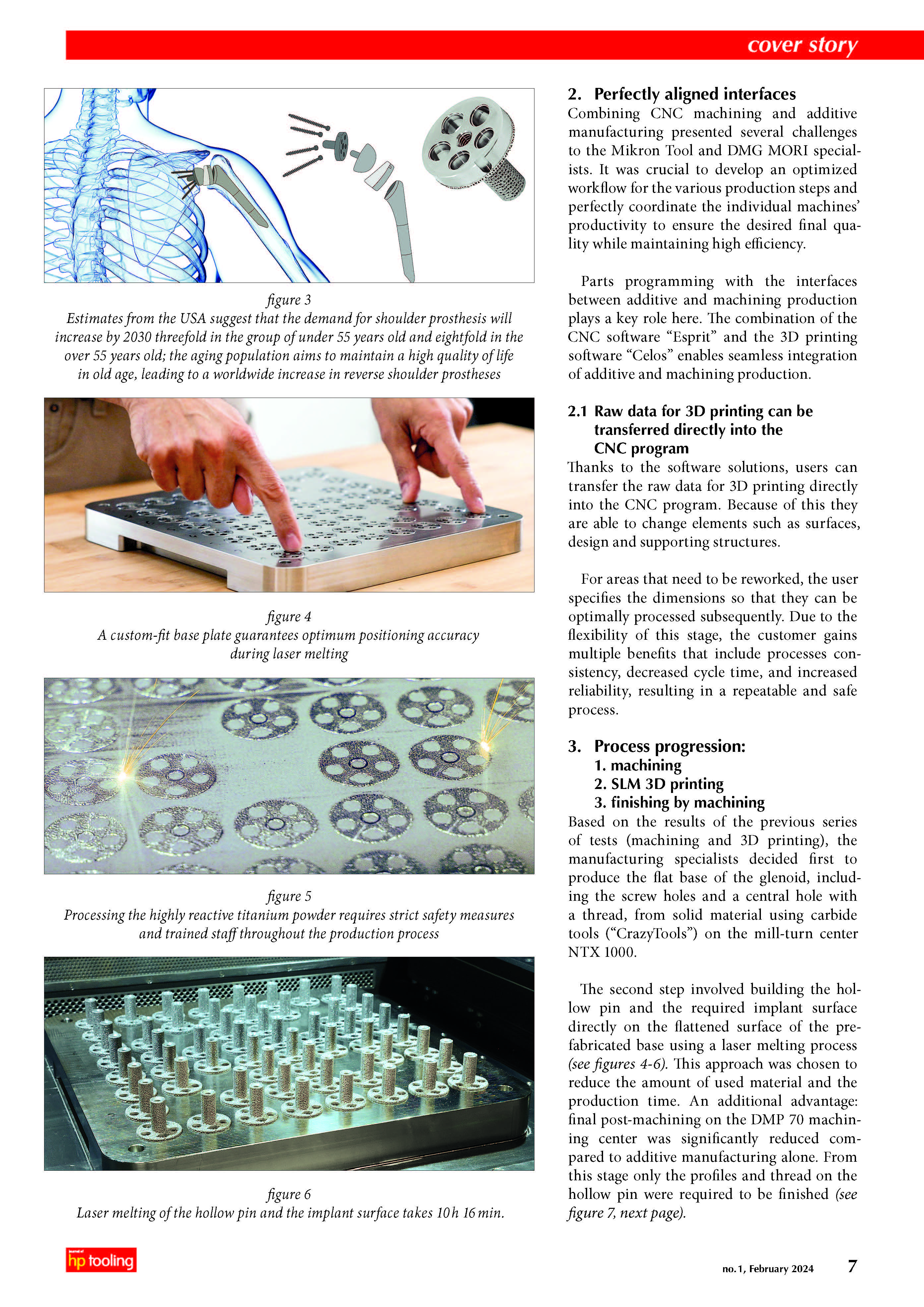
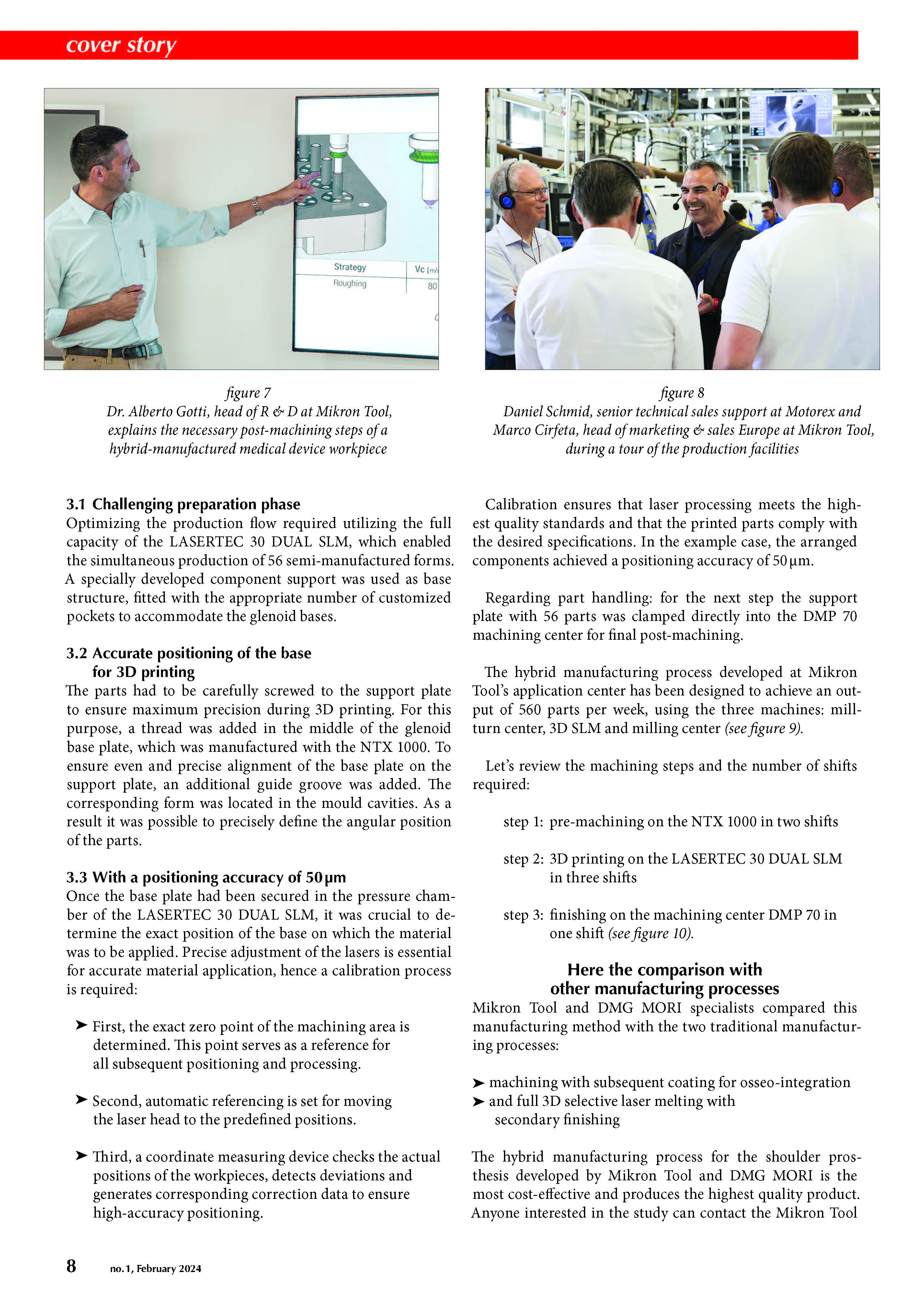
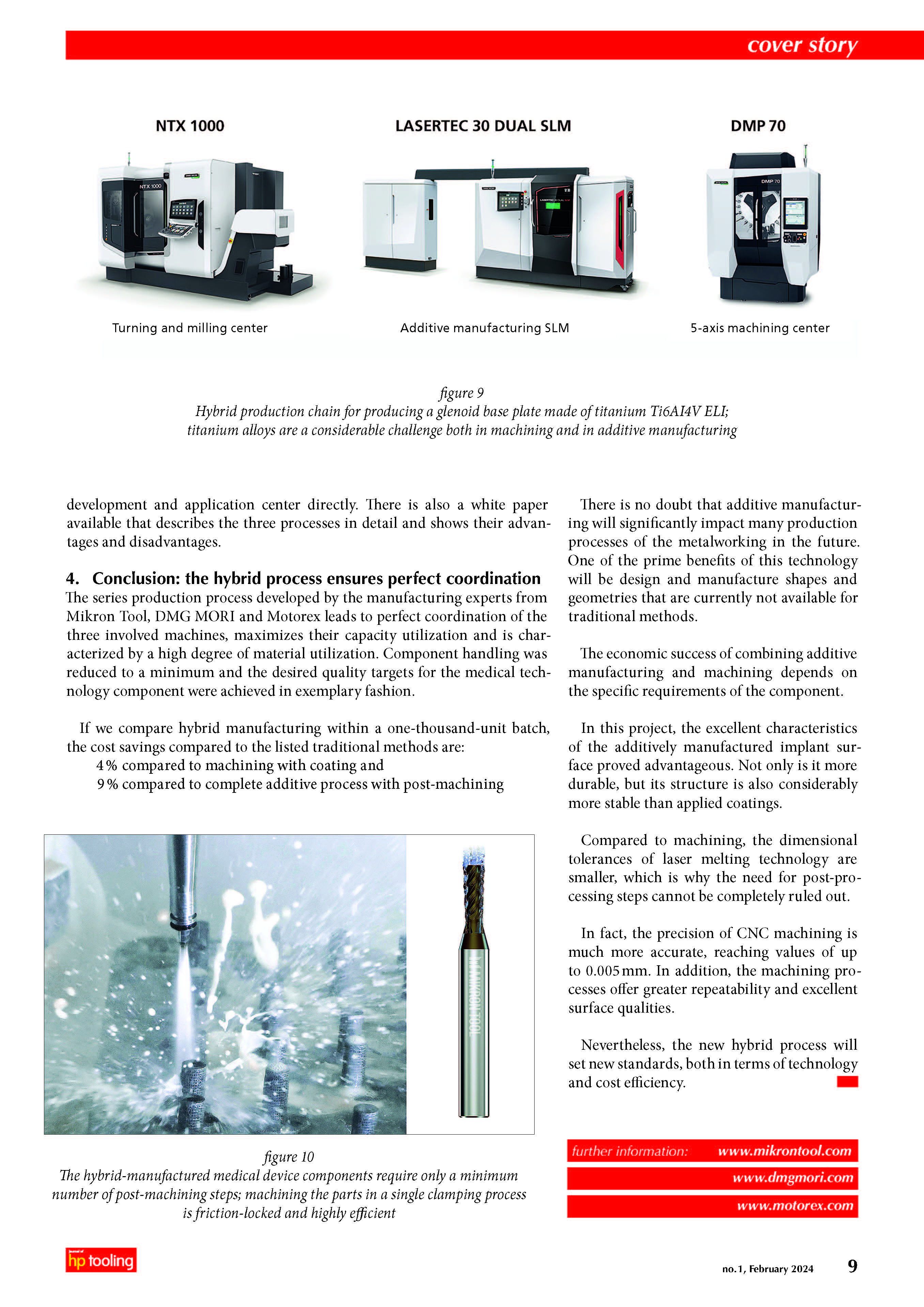